Sheet metal processing process flow
Sheet metal processing is an industry term that simply means processing different metal materials (carbon steel/cold-rolled plate/hot-rolled plate/specc/stainless steel (201, 304, 316) into finished sheet metal parts according to their respective needs, such as (chassis shell, machine tool shell, distribution box, control cabinet, network chassis cabinet, automotive precision parts, etc.).
Common processes in sheet metal processing:
Step 1: Material cutting
Laser cutting is one of the most common cutting methods in sheet metal processing. Based on the size specifications of the finished sheet metal parts, metal stainless steel and other sheets are laser cut into the required size for future use. This process is collectively referred to as cutting.
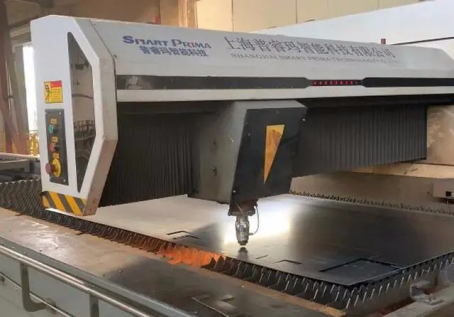
Step 2: Bending
Bending is the process of CNC bending the cut material according to the size specifications of the sheet metal workpiece, and how to prepare it for the next stage of sheet metal welding.
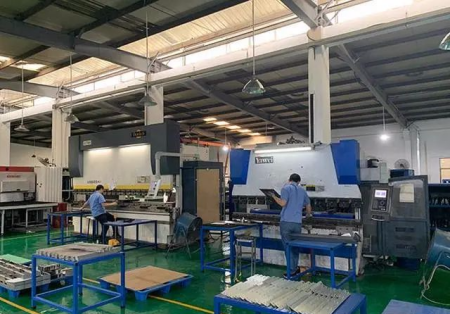
Step 3: Welding
Welding is divided into two methods: manual welding or robot automatic welding. It is a process of welding the cut material into finished sheet metal parts according to the processed finished sheet metal parts. This process also has certain risks and must be operated by experienced masters or completed by robotic hands, with high efficiency and precision.
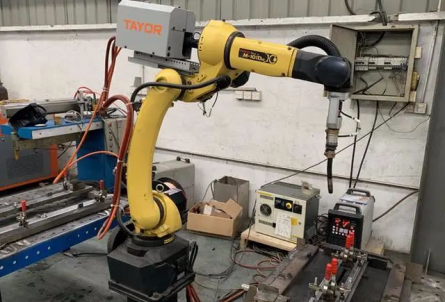
Step 4: Surface polishing treatment
There are also many processes for surface treatment, including hot-dip galvanizing, cold dip galvanizing, galvanizing coloring, powder coating, sandblasting, anodizing coloring, blackening, polishing, and brushing. At the same time, surface treatment is also an important environment in precision stamping sheet metal processing, directly affecting the appearance smoothness, precision tolerance, and other effects of finished sheet metal parts.
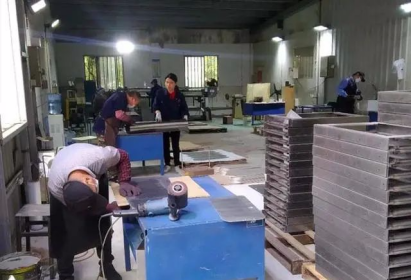
Step 5: Spray electrostatic powder
Powder coating is a process that uses electrostatic forces to adsorb powder coating onto the surface of parts, and after high-temperature curing, forms a hard coating. Powder coating has excellent corrosion resistance and wear resistance, and is suitable for large-scale production. Wearing a "vest" for sheet metal processing parts and replacing them with new ones according to different uses of the sheet metal parts is not only about changing the color, but also the process of powder coating is very rigorous. Temperature, time, powder color mixing, etc. are all crucial.
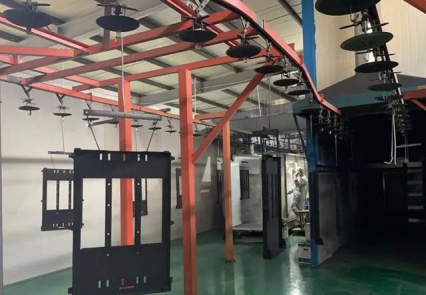
Step 6: Assembly
Assembly is the process of manually assembling and debugging multiple components that have been sprayed, and then packaging them for protection and ease of transportation.
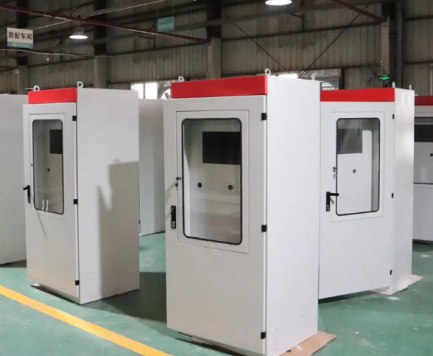
Quality inspection
Quality inspection is an important part of sheet metal processing, which runs through various process links of the entire sheet metal processing, aiming to ensure that the product meets design requirements and quality standards. Common testing methods include dimension testing, surface quality testing, mechanical performance testing, and non-destructive testing.
1. Size inspection
Dimensional inspection is the process of measuring the geometric dimensions of parts using measuring tools to ensure they meet the requirements of the design drawings. Common measuring tools include vernier calipers, micrometers, thickness gauges, and coordinate measuring machines.
2. Surface quality inspection
Surface quality inspection mainly includes the detection of surface roughness, smoothness, and defects (such as scratches and cracks) of parts. The quality of the surface directly affects the appearance and service life of the product. Common testing tools include surface roughness tester, microscope, and visual inspection.
3. Mechanical performance testing
Mechanical performance testing is the inspection of the hardness, strength, toughness, etc. of parts to ensure that they can withstand the corresponding loads during use. The commonly used testing methods include hardness testing, tensile testing, impact testing, and fatigue testing.
4. Non destructive testing
Non destructive testing is a testing technique that uses physical or chemical methods to detect internal defects in parts without damaging the part itself. It is commonly used to detect welded joints and critical components. Common non-destructive testing methods include ultrasonic testing, X-ray testing, magnetic particle testing, and penetrant testing.
Sheet metal processing is a complex and diverse process that involves multiple stages from design, cutting, forming to connection, surface treatment, and quality inspection. Each step has a significant impact on the quality and performance of the final product. Therefore, understanding and mastering the entire process of sheet metal processing is of great significance for improving production efficiency, reducing production costs, and ensuring product quality.
With the development of technology, sheet metal processing technology is also constantly advancing. The application of new processing technologies and automation equipment has greatly improved the accuracy and efficiency of sheet metal processing. In the future, with the further development of intelligent manufacturing, sheet metal processing will move towards greater automation, intelligence, and efficiency, providing higher quality products and services for various industries.
Post time: Oct-23-2024